Do quality glasses last longer than inexpensive ones? Yes and no. Cheap glasses more quickly become scratched, pitted or cloudy. And that's not to mention that glasses are very fragile! "A high quality glass can theoretically be washed about 1,000 times," says Klaus Völkner, Sales Manager Germany of the renowned glass manufacturer Stölzle in the Lusatian region in the German state of Saxony. In reality, however, the situation is different. "A glass only makes it into the dishwasher a maximum of 400 times. Then it usually ends up in the rubbish bin," Völkner says, based on his experience.
IMPROPER HANDLING IS COSTLY
According to Frank Schwarz from the Offenburg warewashing technology specialist MEIKO, the reasons for this are often related to errors in how the glasses are handled. "The glasswasher is sometimes loaded too tightly, resulting in the glasses rubbing against each other during the washing process," explains Schwarz. "Even using the wrong detergent can lead to glass damage. And when being dried by hand, a glass is sometimes dropped on the floor. Another reason is that the kitchen routines are not optimally coordinated, and so on and so forth."
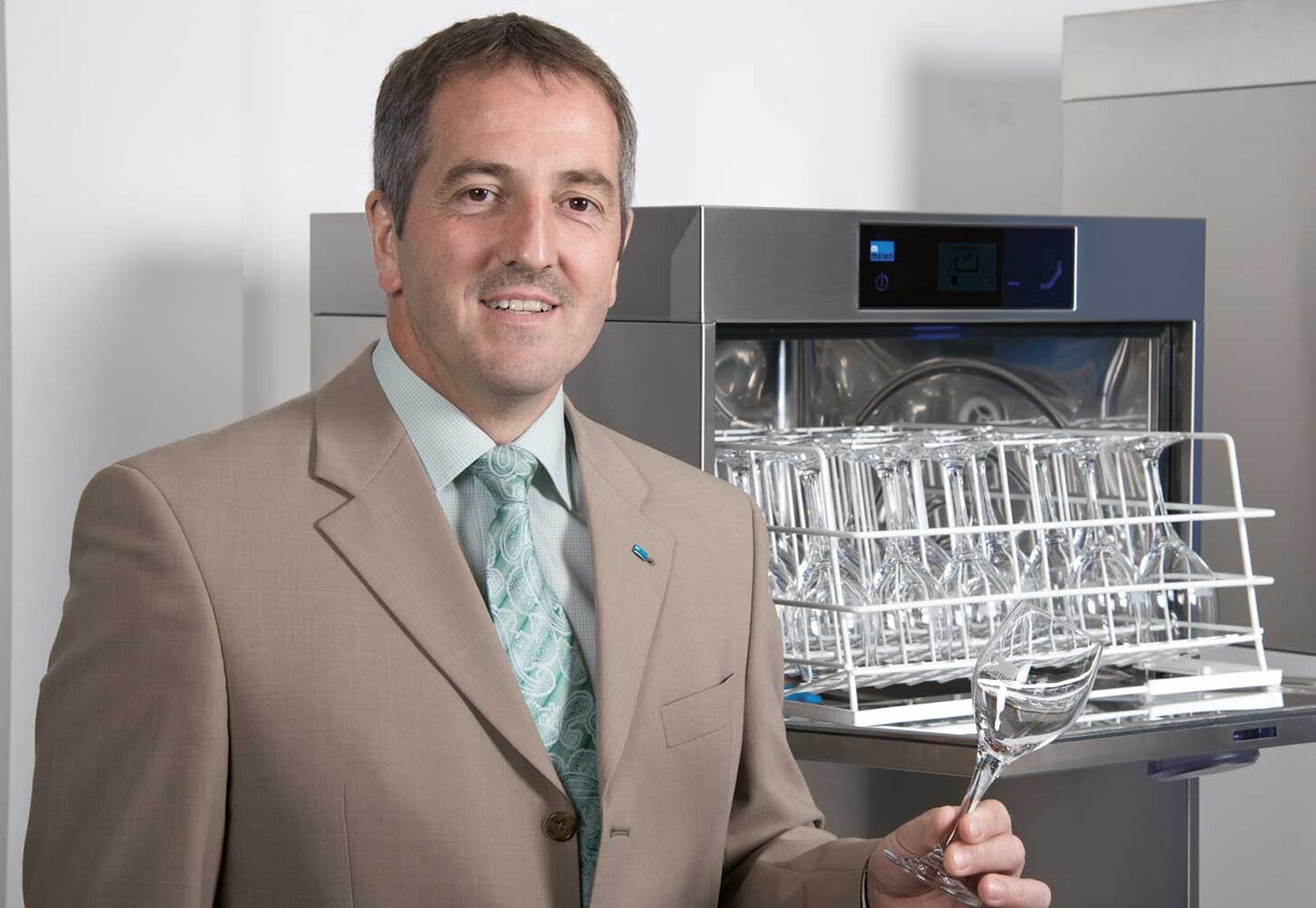
As a result, the costs to the restaurant and hotel operator are immense! "Because glasses," says Frank Schwarz, "have long been an essential part of the value chain, especially since the use of personnel for washing up should not be underestimated. There are two reasons for this. First, drying by hand regularly involves considerable personnel costs (see "Washing costs" below). Plus, you can't make an omelette without breaking eggs. That is to say, glasses are broken because employees either drop them or break the stem while polishing them (see "Glass breakage").
WASHING COSTS: PERSONNEL COSTS ARE EXTREMELY HIGH
While many consider it, none want to accept the fact that employees constitute the crucial cost factor in washing – not the dishwasher, energy costs or something else. In the sample calculation below, personnel costs account for more than 80 percent of the direct costs of dishwashing. This number is based on industry data for Europe that states that employment overhead amounts to about 70 percent of dishwashing costs, taking into consideration ware breakage. The conclusion to be drawn then is that washing costs can only be reduced if it is possible to employ work procedures that prevent the unnecessary handling of glasses and dishes. But that is not enough...
DISTRIBUTION OF WASHING COSTS ACCORDING TO COST ELEMENTS
The costs for one hour of dishwashing using a small undercounter machine break down as follows:
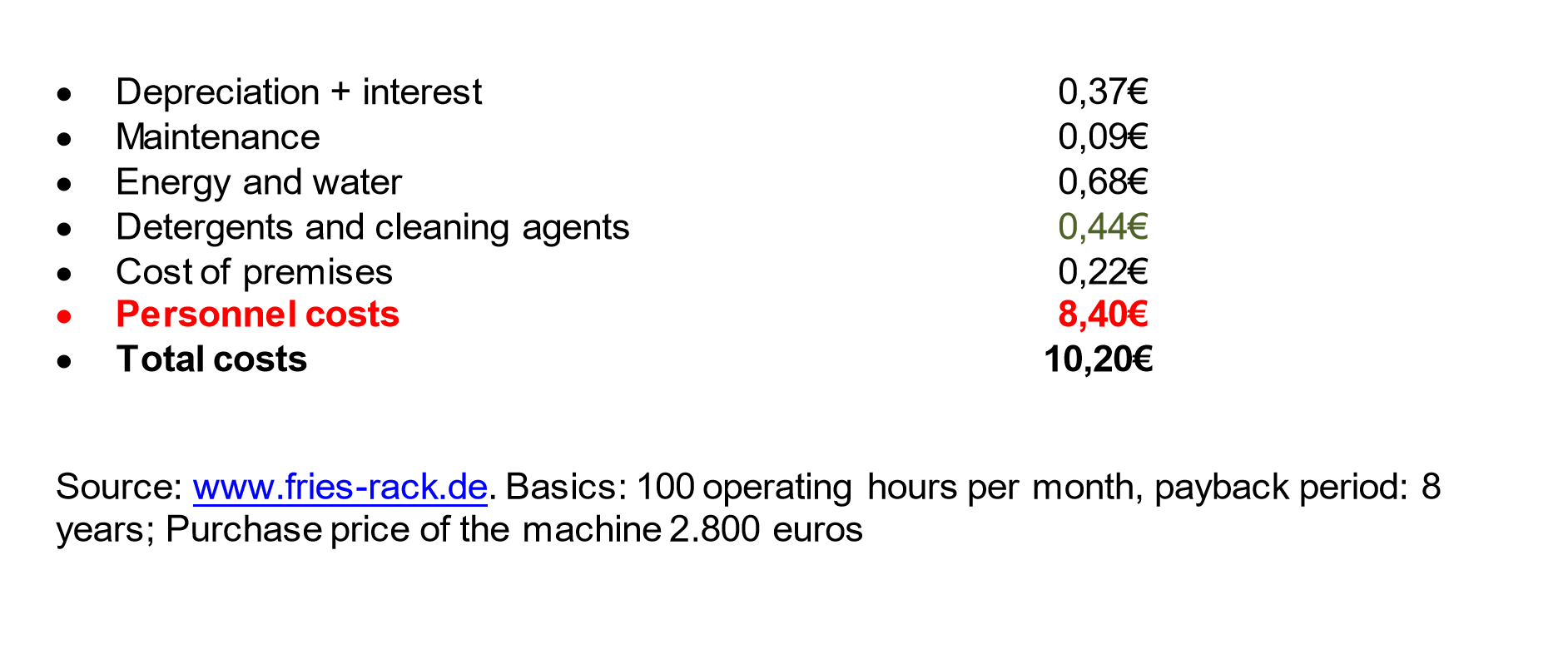
Less glass breakage means lower costs
Eliminate glass polishing, reduce glass breakage and achieve hygienic results. To do this in a restaurant or hotel, you have to take the next step. Engineer Frank Schwarz from the Offenburg warewashing technology specialist MEIKO advises restaurant and hotel owners to use a professional glasswasher that employs a reverse osmosis system and a suitable rack system. "Based on our experience, the use of dishwashers with demineralised, osmotised water and a proper rack system in a professional dishwasher reduces glass breakage from 33 percent (396 euros) to 10 percent (120 euros) per year, explains Schwarz. "One of the reasons for this is that it is no longer necessary to re-polish glasses, because demineralisation eliminates residue build up, which may become deposited on glasses."*
* Q* Source: The sample calculation is from www.fries-rack.de for 600 glasses. Average glass price: 2 euros; cost of 600 glasses: 1,200 euros; empirically determined glass breakage per year: about 33 percent (= 396 euros); using a customised adjustment of the rack in terms of height and by employing an open rack system, a flawless wash and dry result is achieved, while glass breakage is reduced by 10 percent. Re-polishing becomes unnecessary; in addition, the glasses in the rack are secure and protected. Savings potential: approximately 23 percent = 276 euros per year!
Reverse osmosis – what is it?
When water is softened, hardening minerals are replaced by sodium ions. Hard water becomes soft as a result. This effectively prevents calcification of the machine with an increased need for cleaning agents and decalcification.
Partial demineralisation removes only part of the hardening minerals from the water in the the ion exchange process. However, no sodium ions are added to the water, but rather hydrogen ions, because these do not form residues.
Full demineralisation removes all minerals from the water and replaces them with ions that do not form any residues. As with full demineralisation, a reverse osmosis system produces nearly pure, fully demineralised, osmotised water. The water is filtered at high pressure through a membrane that traps almost all of the contents. The tangible benefits of this technology are manifold. This method achieves perfect cleaning results without limescale residue, while also preventing damage to the machine and break downs caused by limescale deposits. This in turn means longer maintenance intervals. In addition, much less detergent and rinse aid are required for washing, which makes the entire washing process much more environmentally friendly. Ultimately, this reverse osmosis system also increases cost-effectiveness, because manual polishing of glasses and cutlery is no longer necessary, resulting in considerably less glass breakage.
REDUCE MANUAL WORK AS MUCH AS POSSIBLE.
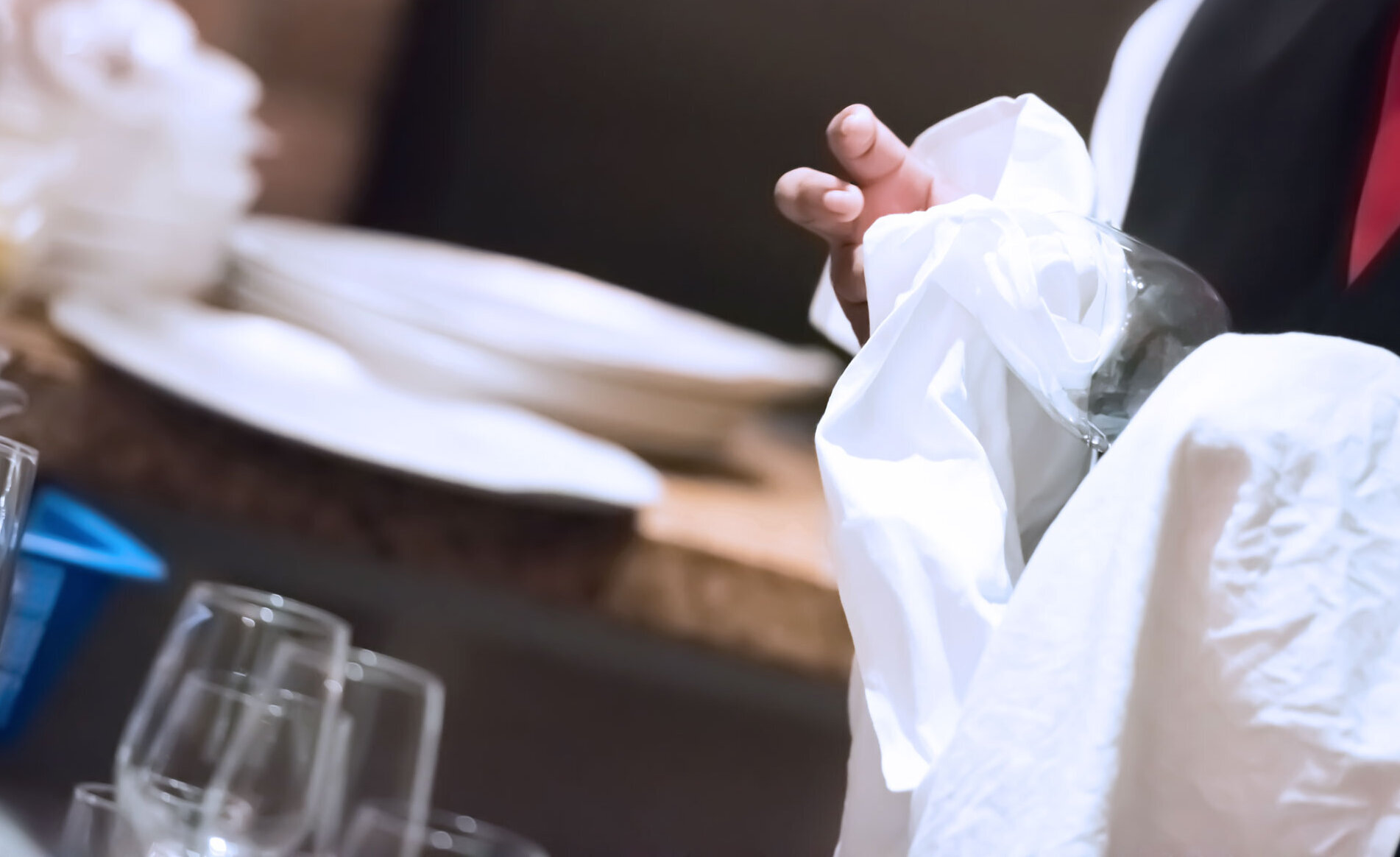
Reducing manual work in the wash up area represents an additional determining factor regarding costs that restaurant owners and hotel managers can influence. How much savings in labour costs can be achieved in washing 600 glasses on daily basis is shown in comparing the following situations.
- After each wash cycle, the glasses are removed from the wash rack and placed on shelves. The rack only serves to wash the glasses.
- If there is a rack system, the glass remains in the rack after washing, i.e. is stored in it.
Based on the assumptions described in the table, this results in annual labour cost savings for the company of around 5,600 euros. This is simply because unnecessary manual work – which is a waste of time, costs money and increases the risk of glass breakage – is avoided.
EFFICIENT GLASS AND COST MANAGEMENT HELPS
There are numerous ways to optimise glass management while reducing costs. In addition to the aspects already mentioned, the planning of the wash-up area and the decision to use optimum dishwashing technology also play an important role. Professional glasswashers, like those from the Offenburg warewashing technology experts MEIKO, lead to significant resource savings in times of rising energy and water prices, boast a high level reliability and deliver a hygienically clean washing result all the time in continuous operation. Or to put it another way, a glass that has been washed using a MEIKO machine is guaranteed not to have to be dried or re-polished by your employees.
