When customers are spending more than €50 for a day pass to a ski resort, the experience needs to match the price. That is something Heinz Schultz knows well. His Group is one of the largest private ski lift operators in Austria – and one of the most successful. This family-owned company in Zillertal does not just bring people to the mountains and spread joy – they have successfully brought together architecture, nature and tourism in way that makes you feel truly alive.
Heinz Schultz's Group of companies proves it can be done. Just look at Mountain View restaurant (Hochzillertal ski area) or at the Spieljoch/Fügen ski area, just two of the seven ski resorts run by the Group. The family's company also employs around 1,000 staff in several other hotels and food service establishments if you needed further proof. All provided happily and successfully.
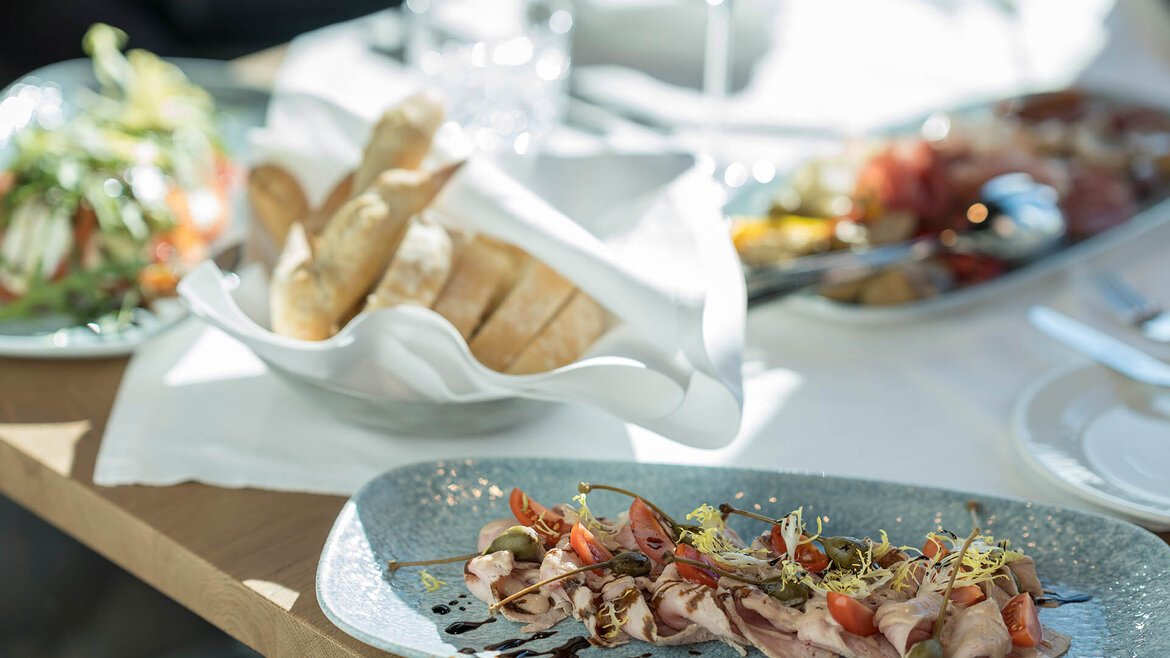
Whether chowing down on a burger, pasta, pizza or a traditional regional dish, eating at, say, Mountain View puts you in one of the most stylish and modern places to be seen in the Austrian Alps. The Schultz Group has taken it all to new heights in Albergo, where you can eat at the highest point on the pistes. All Schultz Group establishments have one thing in common: they strive to provide the customer with the best possible quality. ‘We have made several investments to achieve that over the years,’ recounts Heinz Schultz. He has had the privilege of experiencing how ‘customers are very receptive’ to the efforts made by his family and employees.
Schultz believes the secret to their success is the blend of exciting architecture and mountain landscapes. There is one area where Heinz Schultz does not want any excitement: the quality. And that applies to external partners, too. That is the reason why he chose MEIKO when kitting out the kitchens at Mountain View and Albergo. Hidden conveying technology runs 100 m through Mountain View. Used dishes are carried away reliably, silently and safely, as if by magic! There is no unfinished work to be seen, no used plates or food waste lying around. The operating system can be programmed in house so that if there is a build up of items on the conveyor, the problem can be located immediately.
‘In the design phase, we planned in sufficient access to the conveying technology so that we never have to annoy a customer when someone needs to work on it,’ explains Manfred Fauler who runs MEIKO's business in Tyrol and worked on the design with managers from the Schultz Group. The boss is happy: ‘Warewashing technology is an important factor because it falls under the wider banner of keeping things clean. Dishes have to be perfectly clean and no customer wants to be bothered with used plates and glasses. We have been successful in bringing together the challenging architecture of our building and cutting-edge warewashing technology by MEIKO. MEIKO met every demand, the same demands we make of ourselves, to make sure our customers are happy,’ says Heinz Schultz.
The conveyor is used for empties as well as dishes and a crate of empty bottles weighs over 10 kg! MEIKO's four-roller system provides a non-standard solution for how to manage empties seamlessly.
The central kitchen on the middle floor of the three-storey building in Spieljoch contains the dishwashing area. This is where dishes from the smaller restaurant on the ground floor also come to be washed. They come in a trolley in the lift and make their way into the MEIKO M-iQ flight type dishwashing machine. Soon they will be joined by the dishes from the second floor where an event space is currently being created. These days, the Schultz Group represents the very best in winter sports in Austria and, by his own assessment, Heinz Schultz has achieved that using a very simple mantra: ‘the quality must be higher than the price.’ That, too, is why he chose MEIKO.